Gap-Filler Pads in der dritten Dimension
Es ist eigentlich der Regelfall, dass elektronische Anwendungen aus einer Vielzahl verschiedener Bauteile bestehen. Doch fast immer haben diese unterschiedliche Höhen. Spalten und Toleranzen sind daher unvermeidbar. Um diese auszugleichen, kommen häufig Gap-Filler zum Einsatz. Sie minimieren den thermischen Widerstand zwischen elektronischen Bauteilen und Kühlgehäusen oder Kühlkörpern. Erhältlich sind sie in Form von Fluiden oder als Pads. Erstere haben den Vorteil, dass bei der Verarbeitung sowie im Betrieb nahezu kein Druck auf Bauelemente ausgeübt wird. Dies ist vor allem bei mechanisch sensiblen Bauteilen wichtig. Allerdings müssen diese pastösen Gap-Filler nach der Montage zunächst polymerisieren, also aushärten.
Ein weiterer Nachteil: Nicht jedes Unternehmen will einen solchen Dispensprozess in seine Abläufe integrieren, unter anderem auch, weil die Beschaffung des notwendigen Equipments einen nicht unerheblichen finanziellen Aufwand mit sich bringt.
Die übliche Alternative sind Gap-Filler Pads. Doch lassen sich die bisher üblichen Folien nur mit einem gewissen mechanischen Stress aufbringen. Und jedes Pad füllt mit seiner Dicke nur ein bestimmtes Spaltmaß aus. Sprich: Bei Anwendung einer Materialdicke für mehrere nicht planare elektronische Komponenten mit unterschiedlichen Höhen besteht gerade für empfindliche und sensible Bauteile dann die Gefahr der Beschädigung.
Dank eines neuen Verfahrens können wir nun einige unserer Gap-Filler Pads dreidimensional exakt an Dickenanforderungen anpassen. Der Kunde erhält von uns dabei ein singuläres Verbund-Gap Filler Pad und kann damit alle Dispens- und Aushärteprozesse umgehen. Die Form des Pads ist auf die individuellen Toleranzen und Bauhöhen der Baugruppe auf der Platine zugeschnitten. Daher lassen sich alle Bauteile quasi multiplan anbinden – unabhängig von der Höhe.
Ein weiterer Vorteil des Verfahrens ist die dielektrische Sicherheit der auspolymerisierten Folien, da es keine Gefahr gibt, dass nach der Verpressung Luftblasen entstehen.
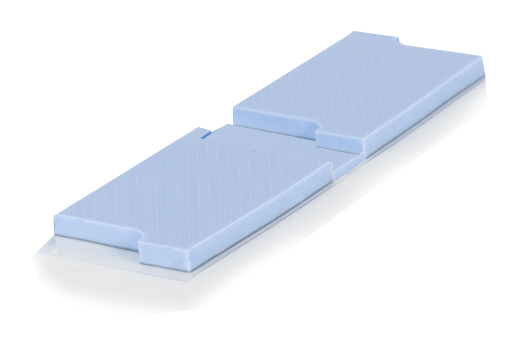